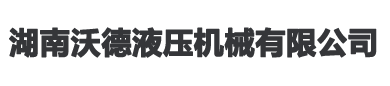

15570700731
歡迎進(jìn)入湖南沃德液壓機(jī)械有限公司官方網(wǎng)站
15570700731
液壓系統(tǒng)的故障現(xiàn)象及原因
發(fā)布時間:2021-06-17
液壓系統(tǒng)故障前通常會有征兆。如壓力不平衡、噪音過大、振動過大、溫升過大、泄漏過大等。如果能及時發(fā)現(xiàn)這些現(xiàn)象并加以適當(dāng)控制或消除,就能減少或避免系統(tǒng)故障。
第一,液壓系統(tǒng)的工作壓力不平衡
壓力不平衡往往表現(xiàn)為壓力不穩(wěn)定、壓力不能上下調(diào)節(jié)、壓力轉(zhuǎn)換延遲、卸載壓力高等。壓力不平衡的原因主要包括以下幾個方面:
1.液壓泵引起的壓力不平衡
1)由于磨損,液壓泵的軸向和徑向間隙增大;
2)泵的“困油”問題未得到滿意解決;
3)泵內(nèi)零件加工裝配精度差;
4)泵內(nèi)個別零件損壞等。
2.液壓控制閥引起的壓力不平衡
1)壓力控制閥中:
(1)先導(dǎo)閥錐閥與閥座配合不好;
調(diào)壓彈簧過軟或損壞;
主閥芯阻尼孔堵塞,滑閥失去控制功能;
主閥芯被污垢卡在開啟位置或關(guān)閉位置;
溢流閥用于遙控時,其遙控連接通道過小或泄漏;
溢流閥用作卸荷閥時,其控制卸荷的換向閥失靈等。
2)在方向控制閥中:
(1)油路切換過快,產(chǎn)生液壓沖擊;
電磁換向閥換向推桿過長或過短。
3.輔助部件引起的壓力不平衡
1)濾油器堵塞;
2)液體流道過小,回油不暢;
3)油粘度太稠或太稀等。
4.其他人
1)機(jī)械部分調(diào)整不好,摩擦阻力過大;
2)空氣進(jìn)入系統(tǒng);
3)油污;
4)電機(jī)功率不足或轉(zhuǎn)速過低;
5)壓力指示器故障等。
二、振動和噪音
振動和噪音是同一個物理現(xiàn)象的兩個方面。液壓系統(tǒng)產(chǎn)生振動時,不僅有一定的振幅和頻率,還伴隨著噪聲。它不僅造成液壓系統(tǒng)的故障,而且對人體健康有害。因此,液壓傳動中噪聲級通常限制在80dB以下。液壓系統(tǒng)產(chǎn)生噪聲的主要原因如下:
1.機(jī)械系統(tǒng)振動引起的噪音
1)皮帶輪、聯(lián)軸器、齒輪和回轉(zhuǎn)體不平衡,滾動軸承滾動體振動;
2)液壓泵軸與電機(jī)軸不同心或聯(lián)軸器松動;
3)管道支撐不良等。
2.液壓泵和液壓馬達(dá)質(zhì)量差引起的噪音
1)零件加工和裝配精度不高;
2)泵的“困油”問題未得到滿意解決,流量和壓力脈動大;
3)軸承質(zhì)量差等。
3.系統(tǒng)密封不嚴(yán)導(dǎo)致的噪音
1)進(jìn)入系統(tǒng)的空氣是液壓系統(tǒng)產(chǎn)生噪聲的主要原因。
4.液壓控制閥故障引起的噪音。
1)溢流閥調(diào)壓彈簧疲勞或端面與軸線垂直度差;
2)閥芯上的小孔堵塞;3)閥芯在閥體內(nèi)不靈活移動;
4)閥體內(nèi)流動的液體對閥壁的沖擊;
5)流動液體的渦流或流體剪切等。
液壓系統(tǒng)
三.空化和空化
空化和氣蝕是液壓元件和液壓系統(tǒng)各種故障的原因之一,尤其是在高壓高速流動的液壓系統(tǒng)中?,F(xiàn)在,這個問題已經(jīng)在液壓元件和系統(tǒng)的設(shè)計中得到充分的重視。對于運維管理人員來說,最重要的是如何有效防止空氣進(jìn)入液壓系統(tǒng)。因此,應(yīng)特別注意以下幾個方面:
1.保持液壓泵各接合面的連接和泵吸入管接頭連接的緊密性;
2.注意油箱內(nèi)的油位不應(yīng)過低,回油管不應(yīng)露出液面;
3.泵吸入管端的濾油器不應(yīng)靠近油位或油箱底部;
4.定期清洗濾油器,防止濾油器被污物堵塞,造成泵吸油不足。
第四,液壓系統(tǒng)的溫升過高
液壓系統(tǒng)的工作溫度一般為30 ~ 55。超過這個溫度會給系統(tǒng)帶來不利影響,從而導(dǎo)致液壓系統(tǒng)失效。油溫高的具體影響是:油的粘度降低,泄漏增加,泵的容積效率和系統(tǒng)效率顯著降低;使不同膨脹系數(shù)的運動副之間的間隙發(fā)生變化,或者導(dǎo)致運動部件失效甚至卡死,或者導(dǎo)致泄漏量增加而降低工作性能;油的氧化加劇,使用壽命縮短;橡膠密封件的加速老化和失效。液壓系統(tǒng)油溫高的主要原因如下:
1.機(jī)械摩擦損失引起的油溫過高
1)液壓元件的加工和裝配質(zhì)量差;
2)相對運動部件之間潤滑條件差;
3)密封質(zhì)量差,調(diào)整過緊。
2.壓力損失導(dǎo)致油溫過高
1)系統(tǒng)中各種閥門規(guī)格過小,管道尺寸過小,彎頭多,無卸荷回路,節(jié)流調(diào)速方式選擇不當(dāng)?shù)取?/p>
2)液壓系統(tǒng)工作壓力調(diào)節(jié)不當(dāng);
3)工作油質(zhì)量太差或粘度太高等。
3.體積損失引起的油溫過高
1)所選液壓泵的額定流量過大,運行時大部分壓力油從溢流閥流回油箱;
2)相對運動部件之間的配合間隙過大,內(nèi)外泄漏大;
3)密封損壞或所有接合面接觸不良導(dǎo)致泄漏;
4)水箱容積太小,散熱條件差,冷卻器有故障。
動詞(verb的縮寫)液壓系統(tǒng)泄漏
泄漏不僅是液壓系統(tǒng)的故障征兆,也是液壓系統(tǒng)的故障,包括外部泄漏和內(nèi)部泄漏。目前,漏油仍然是我國液壓設(shè)備的一個普遍問題,這個問題的解決直接關(guān)系到液壓技術(shù)的發(fā)展和普及。因此,必須采取措施減少泄漏。液壓系統(tǒng)泄漏的主要原因如下:1.接合面加工不良導(dǎo)致的泄漏
1)密封槽過深或過淺;
2)平面密封固定螺孔深度不合適,平面密封部分定位誤差過大;
3)組合密封墊與座孔相互偏離;
4)密封面太粗糙。
2.安裝不良導(dǎo)致泄漏
1)在安裝管接頭時,如緊固螺母與接頭螺紋配合不當(dāng);
2)安裝管接頭時不易對中,存在縮頸不一的現(xiàn)象;
3)緊固管接頭時,使用密封膠帶和密封膠不合適;
4)焊接管接頭時,由于焊接后連接件歪斜,會造成泄漏。
5)再比如安裝V型、Y型密封圈時壓縮力過大;
6)在油泵、油馬達(dá)軸頸和滑閥閥桿外端安裝油封時,唇口會被鑰匙劃破或被彈簧推開,造成泄漏。
3.維護(hù)和材料選擇不當(dāng)造成的泄漏
1)密封圈表面損壞;
2)密封圈材料較軟,密封間隙較大,擠入間隙被咬;
3)油液污染后對液壓部件和密封件的損壞。
從以上分析可以看出,液壓系統(tǒng)的任何故障征兆或故障都不是由單一因素引起的,而是一個非常復(fù)雜的問題。它不僅與部件結(jié)構(gòu)、加工和裝配質(zhì)量有關(guān),而且與系統(tǒng)設(shè)計、安裝和維護(hù)密切相關(guān)。因此,在掌握液壓設(shè)備故障診斷技術(shù)的基礎(chǔ)上,要求人們認(rèn)真處理液壓系統(tǒng)的故障征兆。